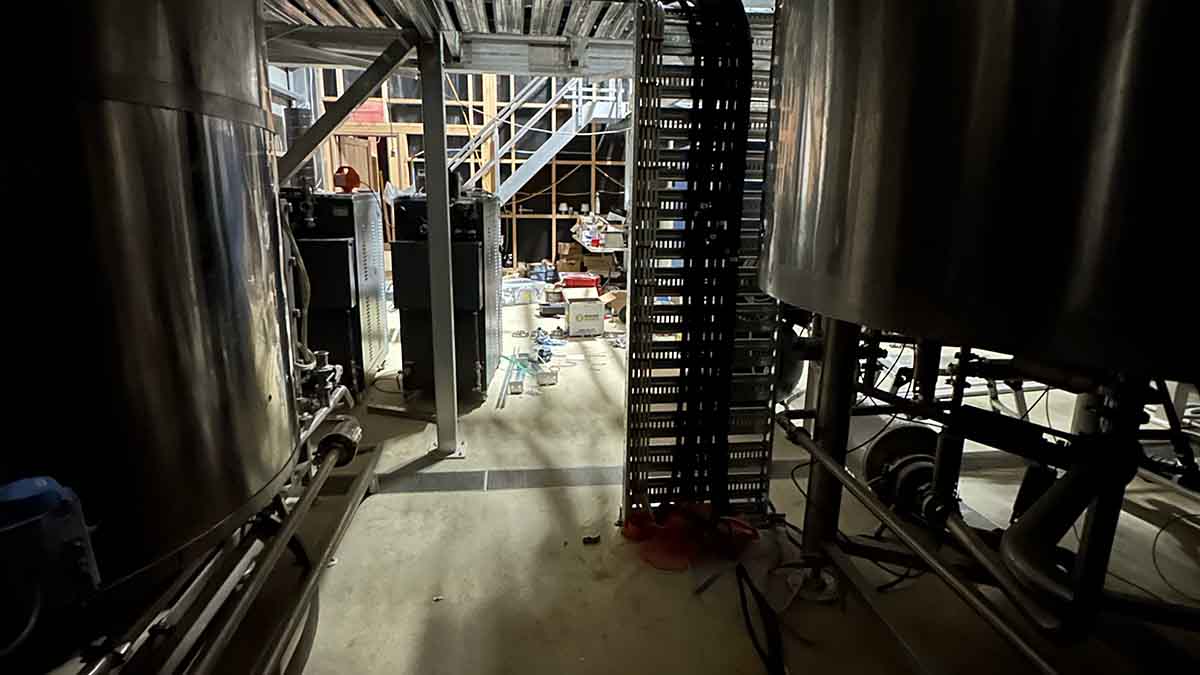
Distillery Build Update 24/4/23
The electric fire steam boilers are getting some attention this week. 3x 120 KW boilers are used to run the brewhouse and still house with a combined output of 600kgs of steam or around 270 HP. This requires some extensive cabling, and in the background picture you can see installed the main power trunk running up to the main board on the gantry above. The cables are 4cm thick for each boiler.
The main board sits behind the process control board and communicates directly to it. From the picture below you can see the 3 boilers being positioned roughly into place. The MPB [ main power board ] for the entire plant is above, the tall cabinet. The control board with the HMI and PLC is the shorter one next to it.
Safety
The reason for the entire buildings power and controls being in one place, is for safety. The control board has a master power switch on it, to shut down the plant, which is also linked to our ethanol detectors. If they sniff ethanol at dangerous levels, they open all the roller doors and then shut down the entire building to prevent a risk of ignition. The vents in the ceiling then force outside air into the building pushing the heavier than air ethanol out of the doors.
Control
Our custom built HMI is running on an intel nuc industrial PC. The touchscreen panel allows the operator to control all elements of the brewing and distillation process. This high level of automation particularly in the brewhouse allows for a consistent wash and spirit profile to be maintained.
The only part not automated are the "head and tails" cuts, and this is still done manually via the spirit safe.